Chemical Vapor Deposition¶
The general CVD process consists of a carbon precursor and a reaction chamber with typically higher temperatures. A pump directs the precursor flow from the right to the left and controls the pressure.¶
Technique¶
Upon all synthesis techniques, chemical vapor deposition is mostly preferred for laboratory scale production of carbon nanotubes. The technique allows synthesis in a controllable environment with constant temperature, an adjustable synthesis pressure and a wide range of variability when it comes to carbon precursors. Gaseous precursors include carbon monoxide[52], methane[53][54] or ethene[55] and various liquid precursors like xylene [56], camphor [57] or benzene [58], or ethanol [2]. In all synthesis routes, metal catalysts are used. While in the early beginnings, only iron, cobalt, and nickel were confirmed to catalyze carbon nanotube growth, CVD has since then shown to apply on a large variety of metals:
Pb [59], Sn, Mg, Al, Cr [60], W [61], Mn [60][62][63], Fe [51][2][64][60][65][61], Co [53][2][66][64][60][61][67], Ni [68][53][43][69][60][70], Cu [71][60][72][67], Mo [52][43][66][60][67], Ru [73], Rh [43][74], Pd [43][60], Pt [43][60][75], and Au [76][60]
Most catalysts today are combinations of different metals as co-alloy catalysts. Although iron and cobalt play a significant role as catalysts, almost all combinations are possible.
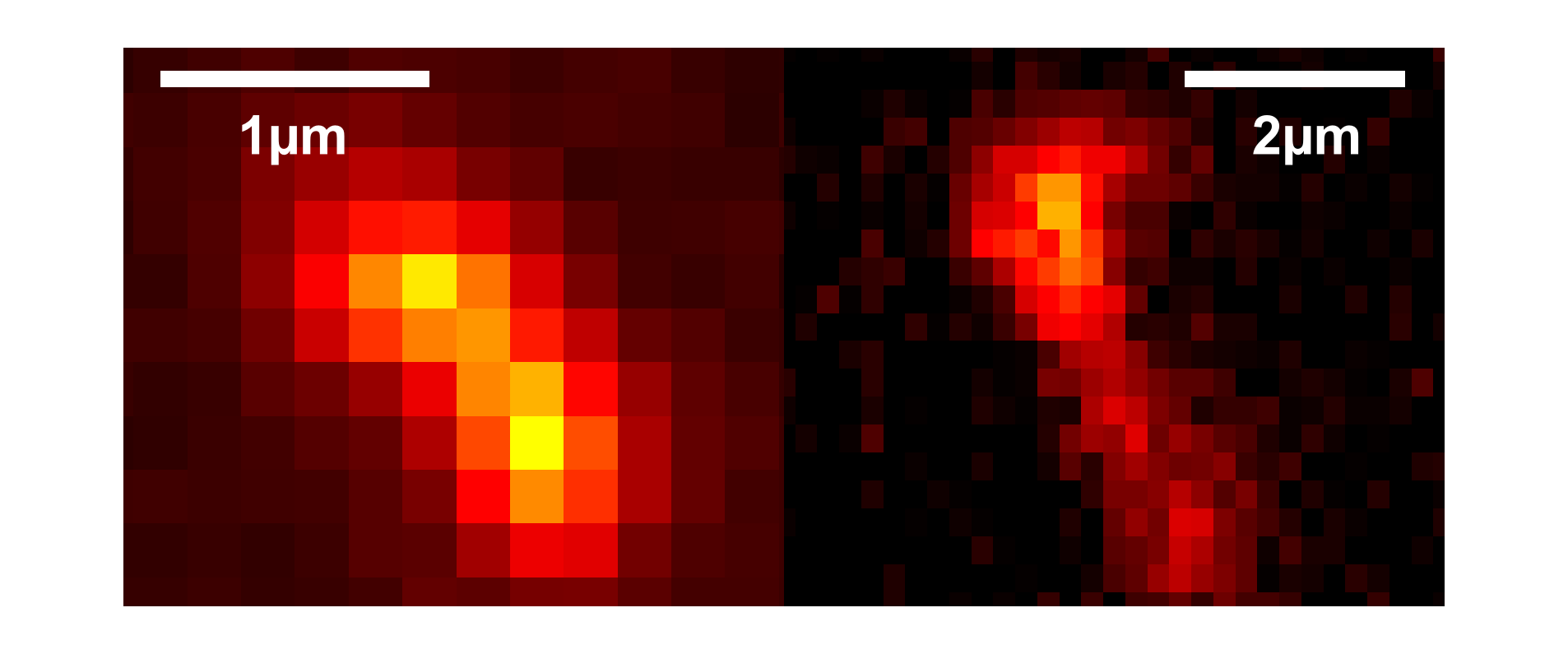
Even unprocessed, raw CoMoCat material[77] like the black sand material (left image) shows overall smaller tube length than the CVD material (right image).¶
Its generally low yield as compared to continuous installations like the commercial HipCo material contrasts to the overall good quality giving carbon nanotubes with fewer lattice defects and higher quantum yields [78]. Single tube lengths of around 5µm are a common result of an unoptimized procedure, which contrasts the 200nm length of the commercially available CoMoCat material[77]. Optimized Processes have even shown that nanotubes from sub-millimeter[79] up to 4cm[65][80] length and more are achievable.
Reactor¶
The setup for Chemical Vapor Deposition from the presented study allows low-pressure CVD, rapid cooldown, and exchange of gas sources during a reaction.¶
The reaction chamber in the presented study consists of an oven that heats the sample for the reaction. The reaction chamber needs to stay evacuated during the whole CVD process to avoid reactions of the produced carbon nanotubes with oxygen which increases hetero atom defects in the graphene lattice.[81][82]
Due to reaction temperatures of 800℃ and more and temperature jumps of around 100℃ per minute, the reaction chamber consists out of quartz, which easily withstands such conditions. A PID controller adjusts the reaction temperature to a value measured at the center of the oven. It is, therefore, crucial to place the sample in the middle of the quartz tube. The oven is placed on rails to allow the proper positioning of the sample. This approach also reduces cooldown time as the oven can be quickly get moved away from the sample and therefore allows laboratory-scale mass production of carbon nanotubes as heat-up is the limiting time factor during synthesis.
The pump evacuates the chamber from the left, and any potentially toxic reaction by-products remain in the cooling trap. A needle valve controls the pressure between the pump and the reaction chamber and allows an exact adjustment of the pressure during synthesis. Additional argon flow as a carrier gas allows increasing the pressure during the reaction. The gas sources are exchangeable, but argon and argon with 3% hydrogen are pre-installed to the system.
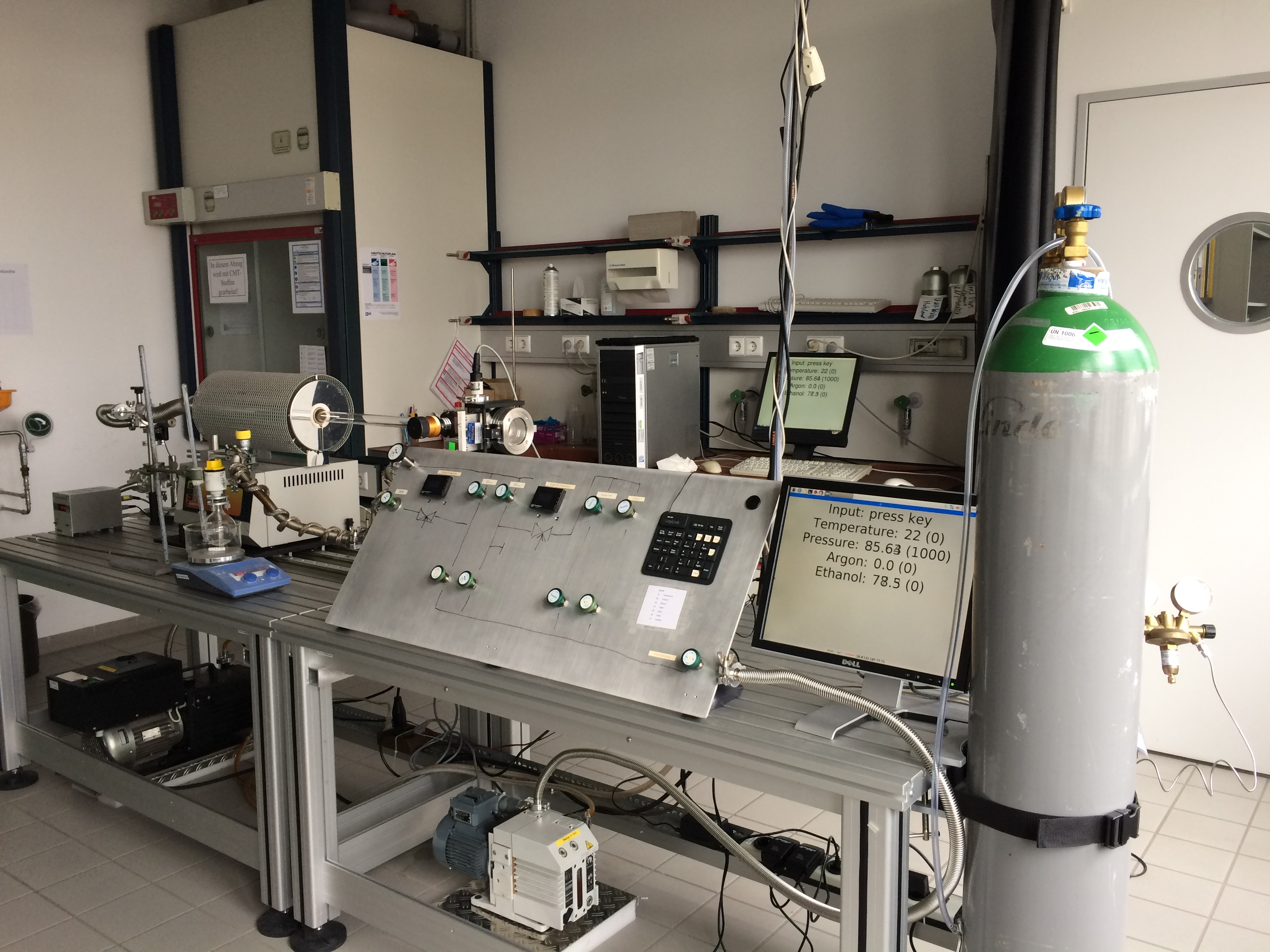
The Chemical Vapor Deposition Reactor consists of an oven in the center of the image and a gas control with different inlets on the right. The pump at the left can achieve constant flow synthesis at 10mbar. The quartz tube connects the gas inlet and pump and allows temperatures of 800℃.¶
The most important part of the reaction is the carbon source, which is plugged in with a glass flask and can hold pre-evacuated solvents. A water bath helps to adjust the vapor pressure, and a needle ventile right after the flask controls the maximum exhaust from the source. A digital flow meter is installed to control precursor inflow. The exchangeable flask and programmable flow meter allow a wide range of carbon sources with vapor pressures of up to around 100mbar.
Nearly all carbon sources that were tested with this setup allow synthesis of carbon nanotubes of fairly small diameters (<1nm). Among the tested carbon sources were methanol, ethanol, n-propanol, i-propanol, butanol, toluene, o-xylene, and p-xylene. Tested hetero-atom carbon sources include acetonitrile, triphenylborane, and triisopropylborate. This large variety of precursors probably also explains the aforementioned early discovery of carbon nanotube synthesis using vastly undefined carbon precursors and metal catalysts.
Due to the chosen setup with a cooling trap, glass flask, and a quartz tube, it is easily cleanable and usable even if potentially toxic, and volatile reaction intermediates are likely to form. The advantage as compared to pure-gas-flow setups is also the low risk of combustion of common gaseous carbon precursors like acetylene.
Alcohol Catalytic CVD¶
Shigeo Maruyama and Shohei Chiashi introduced alcohol catalytic chemical vapor deposition (ACCVD) for the synthesis of semiconducting single-wall carbon nanotubes at the University of Tokyo in 2002.[2] Today, typically ethanol is used as a precursor in this synthesis route for carbon nanotubes. The carbon nanotube community readily accepted this technique due to its simplicity of the setup and its generally secure handling and a-toxic impact of the carbon precursor to western haplotypes[83] if compared to conventional alternatives like toluene or acetylene.
Despite its complexity when it comes to the growth mechanism itself, the combustion into reactive precursors is well studied and understood using theoretical investigations.[84] The liquid combustion product of the ACCVD process is mainly acetaldehyde.[85] More elaborate in-situ monitoring of the reactive intermediates via infrared spectroscopy shows that “ethanol decomposes within 3min and generates ethylene, acetylene, acetaldehyde, methane, carbon monoxide, carbon dioxide, and water”[79]. ¹³C labeling has shown that ethanol reaches the reaction center without splitting into symmetric intermediates like acetylene or ethene. Instead, only the methylic carbon opposite to the hydroxyl group in ethanol is incorporated into the nanotube lattice.[86] Therefore, the reactive asymmetric species of the ethanol combustion process are C-C-OH and C-C-O.[87]. Molecular dynamics simulation studies typically underline the insights into the actual growth process.[88][89]
Not only the mechanism but also the growth conditions are widely understood: There is a close relationship between pressure and synthesis temperature for (A)CCVD which is usually reflected by a phase diagram that relates temperature, pressure, and quality of the synthesized material.[90][4] Hou et al. showed that the temperature for the synthesis of carbon nanotubes using ACCVD ranges between 350 and 1000℃ with a pressure of 10mPa to 10kPa. Such a wide growth range lets the author assume that carbon nanotubes are likely to form during every carbon combustion process that involves metal catalysts. Despite this wide range of acceptable growth conditions, a material with lower defects is typically produced from ACCVD at 750-850℃ with a pressure of 0.1 to 100mbar. Lower pressure is only needed when lowering the synthesis temperature. No-flow techniques [79], where the ethanol flow is turned off during the reaction, allow to achieve lower pressures. While lower temperatures give access to the synthesis of single-wall carbon nanotubes with diameters below 0.8nm, lower temperatures generally also lead to lower sample quality.[78] Smaller diameters grow kinetically at lower temperatures and become thermodynamically unstable at higher temperatures[64] due to their curvature[91][81][92][93]. Therefore, amorphous carbon and defective nanotubes are only avoidable by raising the synthesis temperature.[92][94][90]
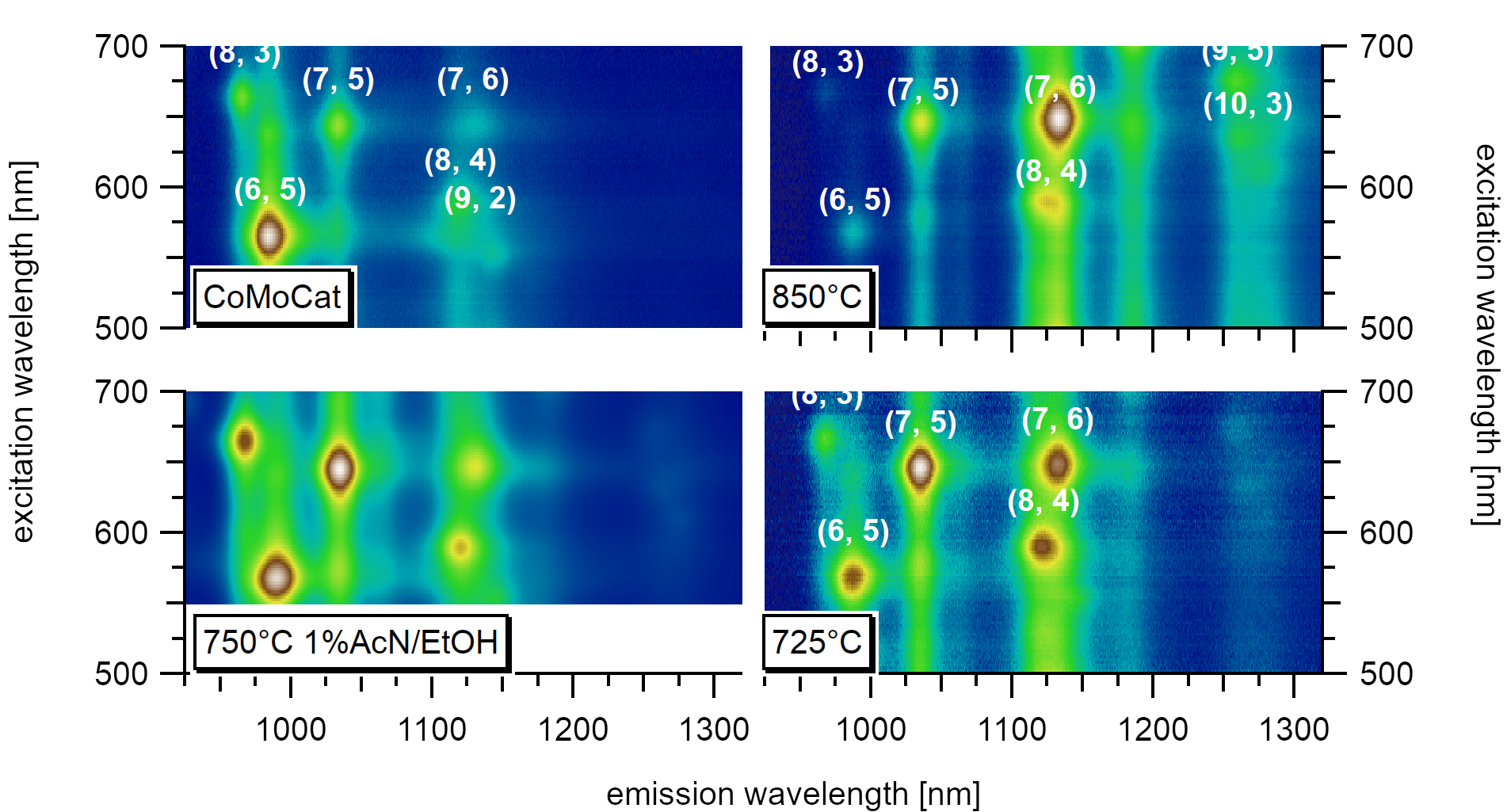
A comparison between commercial CoMoCat Material and as-synthesized CVD material for different synthesis strategies shows the difference in the chirality distribution. The commercial material is post-processed after synthesis to achieve high enrichment in the (6,5) type. It is extensively studied and serves as a reference.¶
Within a constant flow setup like the one presented in this study, the precursor flow mostly determines the minimal achievable reaction pressure. The lower limit of this pressure is at 1-5mbar, and a typical reaction was therefore carried out at 800℃ with a pressure between 5 and 15mbar in a constant ethanol flow environment of 80-300mg/min. At constant pressure, the flow does not play any significant role for reaction times of 10min and below.[85][79]
Notable for the chosen synthesis route is that even though a typical reaction finishes after around 1min, it was carried out for 10min in all experiments to facilitate defect healing due to the reductive properties of combusted ethanol.[95][79][84][87]
The high-temperature trade-off with this setup yields both, good quality and diameters that are in the range of the silicon detector’s quantum efficiency. If low defects and nanotubes between 0.8 and 1.2nm are the preferred synthesis target, these conditions have proven to be best for our CVD setup without the complications that emerge from going to lower pressures.